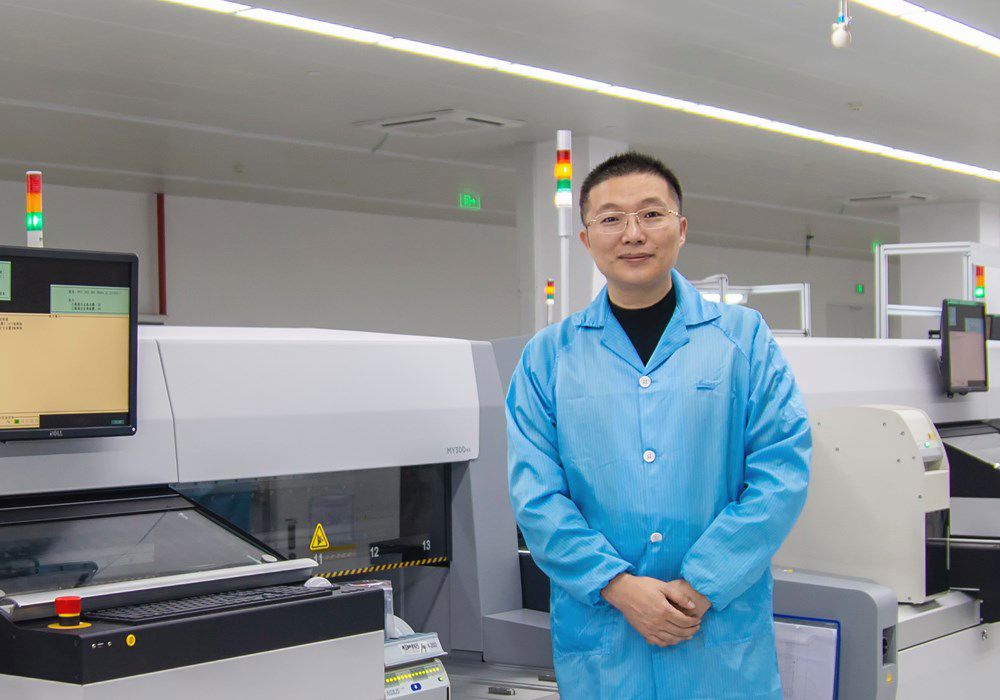
Über den Tellerrand hinausschauen
Wie Wuxi Good Electronics die Grenzen der flexiblen Fertigung verschiebt
Liu Haifeng war nie jemand, der am Status quo festhielt. Als Geschäftsführer von Wuxi Good Electronics Co., Ltd. ist er immer auf der Suche nach den neuesten Produktionstechnologien, neuen Fertigungskonzepten und Verbesserungen beim Kundendienst. Anhand der aktuellen Produktionsstruktur des Unternehmens wird deutlich, wie weit die richtigen Technologien – und eine insgesamt innovative Einstellung – die flexible Bestückung in neue Bereiche vordringen lassen.
Präsentation eines Fertigungspioniers
Bei einem Blick auf Wuxi Good Electronics fällt sofort ein hochgradig flexibles Produktionsumfeld auf, das speziell für die Vielfalt und Qualität einiger der modernsten Elektronikbaugruppen Chinas konfiguriert wurde. Hier können mehr als 10.000 verschiedene hochwertige Bauteile verarbeitet werden, wobei jede Baugruppe die erste ihrer Art sein kann, und überschüssige Material- und Platinenfehler werden einfach nicht akzeptiert. Es ist also kein Zufall, dass hier vor mehr als einem Jahrzehnt der weltweit erste Prototyp einer 5G-Hauptplatine produziert wurde. Dies ist ein Beleg für den Ruf des Unternehmens bei der Nutzung wegweisender, bahnbrechender Technologien.
Von Anfang an wurde Wuxi Good Electronics mit der Zielsetzung gegründet, die Prototyping-Anforderungen der schnell wachsenden High-Tech-Industrie Chinas zu erfüllen. So wurde Mycronic zur perfekten Lösung, vor allem aufgrund der Fähigkeit seiner Pick&Place-Anlagen, alle Arten von Tape-Bauteilen mit automatischer Feeder-Erkennung verarbeiten zu können. „Etwa ein Drittel unserer Produktionschargen besteht aus einer einzigen Leiterplatte, ein weiteres Drittel aus kleinen Prototyp-Serien von zwei bis fünf Leiterplatten“, erklärt Liu Haifeng. „Genau das ist unsere Nische: Wir wollen dazu beitragen, die Forschung und Entwicklung unserer Kunden zu beschleunigen, indem wir ihre Prototypen so schnell wie möglich ohne Abstriche bei der Qualität produzieren. Wir haben schon vor Jahren erkannt, dass Mycronic einen ähnlichen Schwerpunkt hat, und unsere Partnerschaft hat sich mit einem deutlichen Anstieg der Prototypbestellungen von Anfang an wirklich ausgezahlt.“
Erweiterung des Flexibilitätskonzepts
Wie viele der hergestellten Produkte ist auch das Werk einzigartig. Neben einer eher konventionellen Linie für die Serienfertigung sticht vor allem eine Maschine hervor: der Leiterplatten-Pufferturm, ein maßgeschneidertes, mehrspuriges und intelligentes Platinenfördersystem. Hier werden alle im Werk angelieferten Leiterplatten automatisch registriert und über den Siebdrucker, den Mycronic Jetprinter, und SPI zu einem von fünf unabhängigen Bestückungsautomaten weitergeleitet
Abhängig vom eigentlichen Produkt und der Vollständigkeit der Materialaufbereitung können fünf verschiedene Produkte aus dem Leiterplattenpufferturm gleichzeitig auf fünf verschiedene Bestückungsautomaten MY200 und MY300 verteilt werden. Bei einem anderen Produkt können zwei oder mehr Maschinen in Reihe zur Herstellung einer einzigen Baugruppe zusammengeschlossen werden. In beiden Fällen erkennen die Maschinen automatisch alle in der Linie vorhandenen Materialien und nutzen so die Flexibilität und Produktionseffizienz jedes einzelnen Geräts optimal aus.
Mehr Bauteile, weniger Arbeit
Da ein einziger MY300 mehr als 200 Arten von Schüttgütern und Odd-Shaped-Bauteilen gleichzeitig aufnehmen und verarbeiten kann, wurde die Verarbeitung von kurzen Tapes und unverpackten Bauteilen erheblich vereinfacht. „Der Umstand, dass wir kleine Rollen oder Tapes verarbeiten und den Feeder in jeder freien Position anordnen können, ist für unsere Flexibilität absolut unverzichtbar“, erklärt Liu Haifeng. „Dank der Agilis-Feeder ist es so einfach, weil keine Wartung oder Kalibrierung erforderlich ist. Und da verpackte Materialien abseits der Linie geladen werden können, ohne dass ein Bediener anwesend ist, um die Bearbeitung und Bestätigung in der Linie vorzunehmen, hat der MY300 unsere Arbeitseffizienz bei einer extrem breiten Palette von Materialien verbessert.“
Letztlich werden neben der Produktionslinie für große Mengen zwei MYTower-Bauteillagersysteme so zu einer intelligenten Materialflusslösung kombiniert, dass der einfache Zugriff und proaktive Nachschub gewährleistet ist. Ursprünglich motivierte Liu Haifeng die Investition durch seinen Ehrgeiz, den Kunden zusagen zu können, dass ihr Material mit den höchsten Standards der Branche verarbeitet wird, wozu auch strenge Zutrittssicherheit, umfassende Rückverfolgbarkeit und modernste Umweltkontrollen gehören. Im Laufe der Zeit haben die SMD-Tower jedoch weitaus mehr gebracht, nämlich eine deutliche Steigerung der Arbeitseffizienz. „Die Intelligenz der Materialflusssysteme und die Flexibilität der Jetting- und Bestückungssysteme haben uns geholfen, die Anzahl der Umrüstungen, die wir mit demselben Produktionspersonal bewältigen können, zu verdoppeln“, sagt Liu Haifeng. Ähnliche Zuwächse wurden im Rüstbereich erzielt, wo nur ein Bediener eine Arbeit ausführt, mit der früher bis zu drei Vollzeitmitarbeiter beschäftigt waren.
Ein Innovator im Überblick
Das Unternehmen:
Wuxi Good Electronics Co., Ltd.
Standort:
Wuxi, China
Profil:
High-Tech-Hersteller von hochgradig zuverlässiger Kleinserienelektronik (IPC-Klasse 3 oder höher)
Mycronic-Produkte:
Mycronic-Kunde seit 2011, jetzt mit Produktion inklusive Jetprinting-Technologie, flexibler Bestückungsanlage und automatisierten Bauteillagerlösungen von Mycronic
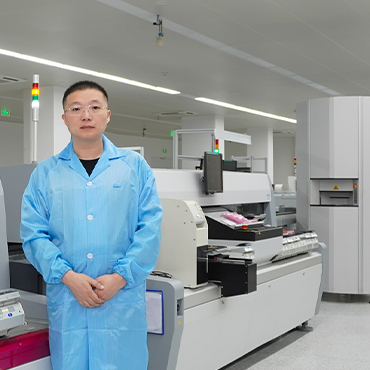
Schnellere Programmierung, bessere Qualität
In der anspruchsvollen Welt der schnellen Prototyp-Fertigung sind erfahrene Bediener natürlich nach wie vor unverzichtbar für eine hohe Produktivität. Bei besonders schwierigen Bauteilen nutzen die Bediener eine Funktion zur Unterstützung der Bestückung, die es ihnen ermöglicht, die Bestückungsmaschine im Sinne einer bestimmten Bauteilanordnung zu führen und so den vollständigen Programmierprozess mit Gesamtansicht zu vermeiden. Dank der Steuerung mit geringem Kraftaufwand, z. B. bei der Montage dünner und empfindlicher Bauteile, konnten die Produktionsmitarbeiter auch das Nachlöten einzelner Kontakte praktisch eliminieren.
Somit wurde der Beweis erbracht, dass die kürzeste Distanz nicht eine einzige Linie ist.
Mit all diesen Qualitäts- und Effizienzvorteilen geht eine extrem hohe Produktionsflexibilität einher. Vom Prototyp der ersten Charge über die Kleinserienfertigung bis hin zu Baureihen mit Hunderten von Leiterplatten ist das gesamte System so programmiert, dass es sich dynamisch anpasst, die Produktion koordiniert und die Bestückungskapazität kombiniert, sobald die erste Leiterplatte erfasst wird.
„Unsere hochflexible Gestaltung der Produktionslinie hat den schnellen Wechsel von kleinen Chargen und mehreren Varianten erst ermöglicht“, erklärt Liu Haifeng. Damit wurde das hartnäckige Problem der geringen Auslastung der Produktionslinien gelöst und unsere Produktionskapazität und -effizienz erheblich verbessert. Es war viel harte Arbeit erforderlich, aber diese nichtlineare Kombination von fünf Bestückungsautomaten hat unsere Anlagenauslastung deutlich verbessert und die Einstandskosten der Produktionslinie gesenkt.“
Aufgrund der Stärke des Unternehmens im Bereich der schnellen Prototyperstellung verzeichnet das Team von Liu Haifeng eine zunehmende Integration mit den R&D-Teams der Kunden. Um diese Entwicklung zu unterstützen, wurde kürzlich ein Design-for-Manufacturing (DFM)-System mit den Mycronic-Geräten und der MYCenter-Software verbunden. „Wir machen weiterhin Fortschritte bei der Verkürzung des Reservezyklus für unsere Kunden“, sagt Liu Haifeng. „Wir können mehr Umrüstungen vornehmen und mehr Leistung erzielen, so dass die Kunden jetzt in der Fabrik auf ihren Prototyp warten können. Das wird bei uns gern als „Prototyp-to-go" bezeichnet“, sagt er mit einem Lächeln.
Partnerschaft für die Zukunft
„Ein großer Teil dieses Erfolgs ist auf die großartige Zusammenarbeit zwischen uns und Mycronic zurückzuführen“, fährt er fort. „Wir haben ähnliche Ambitionen, wir lernen gemeinsam, und ihre Vertriebsmitarbeiter und Anwendungstechniker sind alle mit unserer Branche vertraut. Ich betrachte das lokale Mycronic-Team als meine Kollegen, da die Interaktion und Kommunikation großartig ist. Solange wir uns auf unser Nischengeschäft konzentrieren und gemeinsam voranschreiten, spielt es keine Rolle, was unsere Mitbewerber mit größeren Serien tun.“