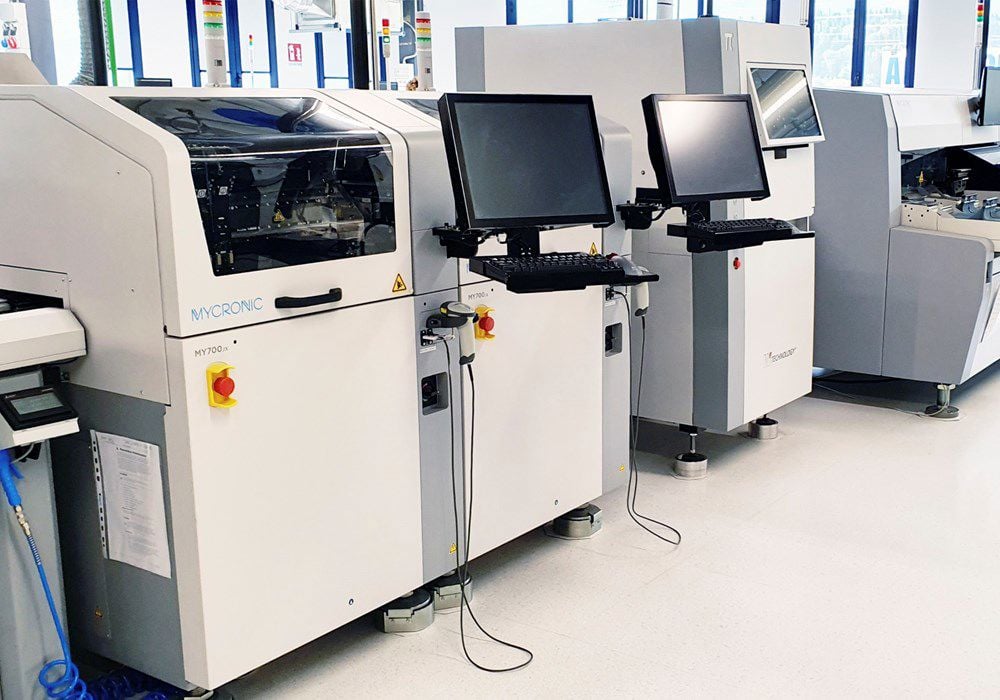
Umsetzung von Leistungsdaten
Verbesserung der Abwurfraten-Analyse und des Linien-Balancing mit MYCenter Analysis
Als innovativer europäischer Auftragsfertiger ist DF Elettronica entschlossen, die Grenzen der Automatisierung kontinuierlich zu erweitern. Ob Inspektion, Rückverfolgbarkeit, Materialtransport oder Prozessoptimierung – der Einsatz hochmoderner Technologien steht seit vielen Jahren im Mittelpunkt der erfolgreichen Produktionsstrategie dieses Unternehmens. MYCenter Analysis ist lediglich der neueste Schritt auf der Suche nach einem optimalen, hochflexiblen Produktionsumfeld.
DF Elettronica befindet sich am nördlichen Stadtrand von Florenz in Italien. Das Unternehmen ist ein relativ kleiner EMS-Dienstleister mit etwas mehr als dreißig Mitarbeitern. Aber durch die Kombination der richtigen Mitarbeiter mit den richtigen Produktionstechnologien geht das Unternehmen weit über seine eigentliche Liga hinaus und bedient eine Vielzahl führender europäischer Kunden aus den Bereichen Biomedizin, Beleuchtung und Telekommunikation.
Investition in Agilität
„Unser Eigentümer glaubt fest an die Fabrikautomatisierung und die Anwendung hochmoderner Technologien“, sagt Patrizio Sorace, Produktionsleiter bei DF Elettronica. „Er hat schon früh in einen Vakuumkammerofen investiert, der ein entscheidender Faktor bei der Herstellung hochwertiger LED-Beleuchtungssysteme war. Als er sah, dass er zu viel Zeit damit verbrachte, Kassetten mit Leiterplatten von der SMT-Fertigung zur Endmontage zu transportieren, investierte er in autonome Transportsysteme. Gleiches gilt für 3D-Inspektionen, Lasermarkiersysteme und Flying-Probe-Testanlagen, die sich für unsere Kunden ausgezahlt haben. Als er von MYCenter Analysis hörte, erkannte er sofort das Potenzial, viel Zeit und Arbeitsaufwand einzusparen.“
In der Produktion wurde eine bessere Visualisierung der Pick&Place-Leistungsdaten am dringlichsten benötigt. „Als es um das Linien-Balancing von Maschinen ging, wollten wir schneller erkennen, wo Verbesserungspotenzial bestand“, erklärt Sorace mit dem Hinweis, dass dies insbesondere auf die Großserienproduktionslinie zutrifft. „Einige dieser Chargen können die Linie mehrere Tage lang besetzen, so dass selbst fünf oder sechs Sekunden Gewinn pro Leiterplatte ziemlich viel ausmachen.“
Das zweite Ziel bestand darin, die Ursachen von Bauteilabwurf und Verschwendung schneller zu identifizieren, was allzu oft mit einer komplexen Ursachenanalyse verbunden war. „Wir fragten uns: Ist das ein Feeder-Problem? Oder ein fehlerhaft programmiertes Gehäuse? Ein verschmutztes oder defektes Werkzeug?“, erinnert sich Sorace. „Es gibt Unmengen von Variablen, also wollten wir wirklich eine Art statistische Analyse, aus der hervorgehen würde, ob ein Großteil der Probleme mit einem bestimmten Werkzeug oder einem bestimmten Bauteil zusammenhängt.“
Die Stärke der Analyse
Als Sorace und sein Team die Gelegenheit erhielten, MYCenter Analysis in einem Beta-Test auszuprobieren, zögerten sie nicht. „Wir haben uns sehr gefreut, als wir die erste Version von MYCenter Analysis erhielten. Genau das war unser Ziel: die statistische Analyse zu erhalten, die wir brauchten, damit die Bediener die Ursachen von Abwurfproblemen finden konnten. Jetzt können sie mit einem einfach Klick die Bilder eines Werkzeugs aufrufen, das gereinigt werden muss, und sehr schnell die richtigen Schlüsse ziehen. Sie können das System auch von zu Hause aus verwenden, um beispielsweise ein problematisches Werkzeug zu identifizieren. Natürlich ist noch nicht alles gelöst, aber wir machen auf jeden Fall Fortschritte.“
Das große Ganze im Blick
Wie in vielen kleineren Firmen haben Sorace und seine Kollegen ein breites Aufgabenspektrum. Als Produktionsleiter beaufsichtigt Sorace die Infrastruktur, überwacht die Gesamtleistung der Maschinen und ist für potenzielle Verbesserungen im Arbeitsablauf zuständig. Zu anderen Zeiten kann er an der Produktionslinie aushelfen, Gehäuse programmieren und sonstige technische Aufgaben übernehmen. „Das ist typisch für eine Firma wie unsere“ erzählt er. „Wir sind alle so sehr mit mehreren Maschinen und Prozessen beschäftigt, dass es manchmal schwierig sein kann, das große Ganze zu sehen. Hier kann eine Software wie diese einen Unterschied machen und uns den dringend benötigten statistischen Überblick geben.“
Für die Zukunft hat der Eigentümer des Unternehmens vorgeschlagen, einen Mitarbeiter abseits der Linien mit mehr Befugnissen in Bezug auf die Produktionsüberwachung und -verbesserung zu beauftragen. Diese Verantwortung werden höchstwahrscheinlich Sorace und MYCenter Analysis übernehmen. „Unser Bediener hat einfach zu viel zu tun", weiß Sorace, „deshalb kann ich jetzt die Software nutzen, um ihn zu unterstützen. Ich kann mir leicht ein Szenario vorstellen, in dem wir einen Auftrag mit hohem Volumen erhalten, wobei jede Linie ihren eigenen zugeordneten Bediener hat und sich jemand abseits der Linien auf die Produktionsüberwachung, -analyse und -verbesserung konzentriert. Das ist unsere Zielsetzung.“
Leistungssteigerung
Auf die Frage, wie die Vorteile der MYCenter-Analyse quantifiziert werden können, räumt Sorace ein, dass dies eine Herausforderung in der High-Mix-Produktion sein kann, bei der es darum geht, eine endlose Reihe von Variablen ständig unter Kontrolle zu haben. „Unsere Produktion variiert von Auftrag zu Auftrag so stark, dass es wirklich schwierig ist, einen Vorher-Nachher-Vergleich anzustellen“, erklärt er. „Und dieses Jahr ist aufgrund der Pandemie alles anders, so dass eine vergleichende Analyse nicht sehr realistisch wäre. Aber unseren Erfahrungen zufolge hat uns MYCenter Analysis sehr geholfen, insbesondere in Bezug auf die Ausschussanalyse und den Linienausgleich bei größeren Aufträgen. Auf lange Sicht werden wir es auf jeden Fall nutzen, um mehr Daten-Benchmarks zu setzen und ältere Daten mit der aktuellen Leistung zu vergleichen. Wenn wir die Automatisierung weiter erhöhen, unsere Fähigkeit verbessern, sehr schnell zwischen den täglichen Aufträgen umzuschalten, und viele Kunden sehr schnell mit hoher Qualität und möglichst geringen Kosten bedienen können, dann wissen wir, dass wir auf dem richtigen Weg sind.“