Surprising insights
MYCenter Analysis reveals new improvement possibilitiesFor Allelektronik in southern Sweden, the new MYCenter Analysis dashboard came as a real eye-opener. Having spent more than a decade optimizing production for a single customer, Production Manager Mats Landström was thrilled to see things from an entirely new perspective. “We really didn’t know if the software would be useful at first,” he says. “Now we can’t live without it.”
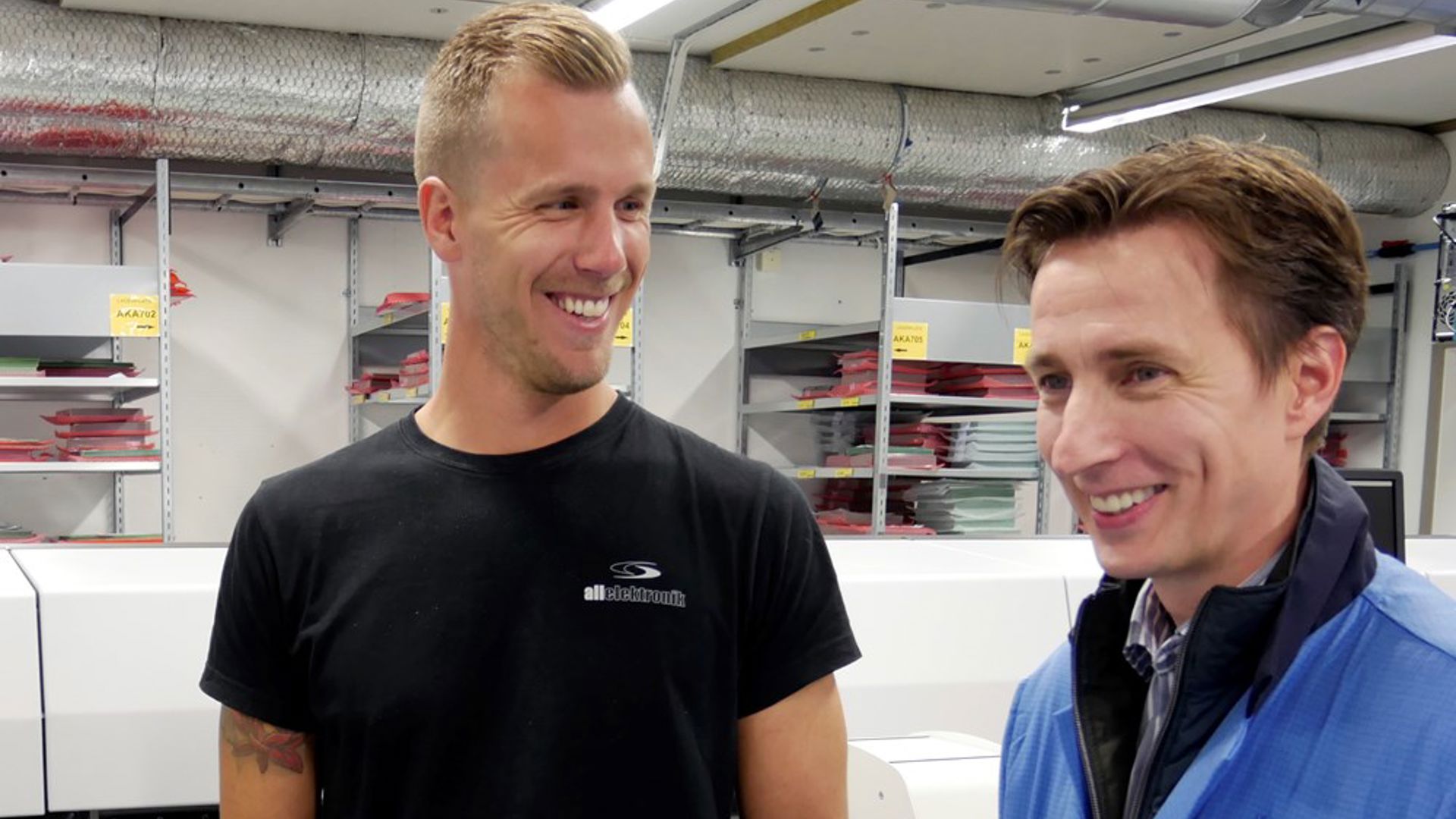
Like many manufacturers, Mats knows his production line inside and out. At the same time, he was curious whether there might be room for further improvement. “It’s easy to get a bit too close with your machines and to think you’ve optimized them in every way possible,” he says. “Still, I wondered: could there be something we’re missing?”
Visualizing line performance
Three months later, he continues to find new answers to this question every day with the help of MYCenter Analysis. “When you see it visually on the screen it’s obvious where the problem is. You’re much quicker to see if a line is underperforming.”
“There’s usually three of us on the floor with the dashboard up on a big screen,” he continues. “So while you’re changing a reel or something you can check the dashboard and see rejects, utilization, and so on. We really try to get the most out of everyone’s efforts, including my own, so with this software we can all multitask and keep an eye on things.”
Faster problem-solving
On the biggest jobs, the ability to quickly identify the causes of rejects alone can save the company’s operators a considerable amount of work. “It’s saved a lot of time for our operators,” says Mats. “Instead of searching for specific problems they can focus more generally on maintaining the line. With a big batch of, say 3,000 boards, you could maybe save three hours if you’re not hunting for problems. Add that up over a year and it amounts to a lot of time.”
Optimizing for the future
Now that the MYCenter Analysis dashboard is integrated into his team’s daily routines, the insights it’s revealed have caused Mats to rethink the configuration of his production line in a long-term perspective. “Our MY300 Trilogy line is considerably more stable now,” he says confidently. “Any unbalance in the line is more visible, and now we have a better understanding of which capabilities are needed in each machine. This is really a big help as we plan for the future.”