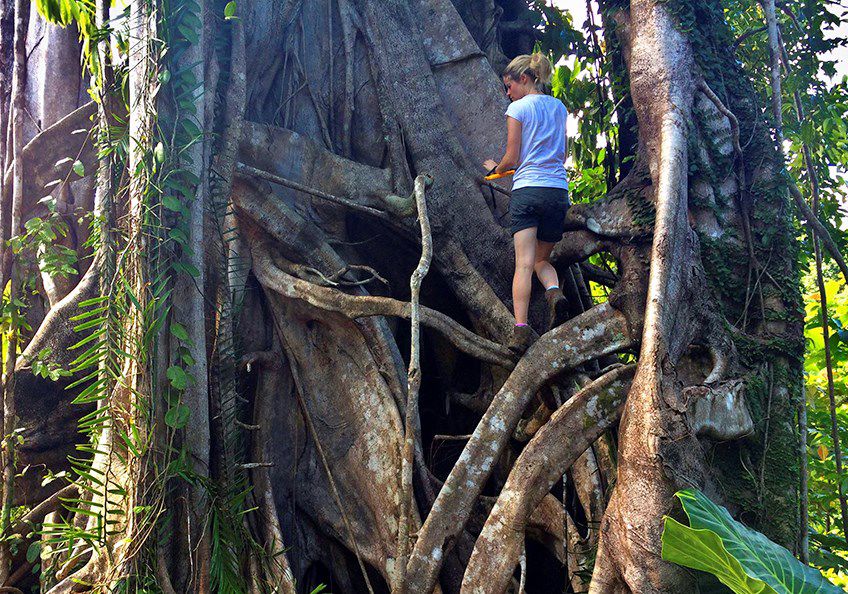
A high-tech future down under
Building a smarter platform for innovation in Australia
At its headquarters in a high-tech industry hub in Brisbane, Australia, Elexon Electronics is investing in the future of advanced local manufacturing. For CEO Frank Faller, this means finding new solutions to turn ideas into products faster, smarter and with the highest quality.
Building some of Australia’s most challenging electronics Elexon has engineered and manufactured a diverse array of sophisticated products since the company’s founding in 2006. Together with its sister companies, it has carved out successful niches in advanced monitoring systems for mines and devices for monitoring the ultrasonic echolocation calls of bats, together with many other products developed for direct customers.
“We strive to be the best manufacturer for our sister companies, and for other businesses around the world,” says Frank.
Continuous improvement
To keep business thriving in Queensland, however, Elexon also needs its equipment to remain at the leading edge. “As part of our ambitious growth plan, we decided to invest heavily in the latest technologies from Mycronic,” Frank explains. “To double our output and reduce our transition to manufacturing time and costs by 30% — all of this requires state-of-the-art intelligent factory solutions.”
Thanks in part to local government funding assistance from the Made in Queensland grant program, Frank and his team were able to acquire what they saw as the best available equipment for the task: a MY700 jet printer with two MY300 pick-and-place machines, tower storage solutions, a vapor phase vacuum reflow oven, X-ray inspection system and a set of highly automated conveyors as part of an integrated Mycronic 4.0 solution.
A major leap forward
Remarkably, most of the company’s business goals have been achieved after fewer than six months with the new equipment in operation. These include doubling the company’s production output, substantial cost reductions and a one-hundred percent record of delivery, in full and on time, for the past three months.
Perfecting quality management
Elexon’s management was especially keen on ensuring that the new line enabled the highest standards in quality management. “Now we can collect more refined quality data, improve our monthly reviews and address any issues,” says Frank. “One of our recent production runs, a complex CPU board that has been in production for over seven years, had a first-pass yield of 100% – something we have never been able to achieve before.”
The complete package
Among other improvements in NPI turnaround times, BGA capabilities and production planning, Frank is most thrilled about all the new possibilities enabled by the new production line.
“The most exciting thing is that we really have the complete package, not just a lot of islands and machines,” he explains. “Everything fits together – the communication between the towers, the proactive replenishments, the scheduling. You can scan the product’s bar code and it loads the program for the whole line without risk for human errors.”
Data-driven innovation
Today, Frank feels the company is now better equipped than ever to bring unique value to local and export-based customers throughout Australia. “The world is becoming more data-driven,” he concludes, “and that’s the beauty with this system. We can convert CAD data straight into solder paste and pick-and-place programs. Through the web interface, anyone in the business can get access to quality and performance data. There is much more data available to refine the performance of the machines and to visualize and share the increases in productivity with the production team.
Made in Queensland
Made in Queensland supports small to medium manufacturers to increase international competitiveness, productivity and innovation via the adoption of new technologies.
To date (2020), through Rounds 1 and 2, the MiQ program has supported 75 advanced manufacturing projects across the State, generating 930 new jobs over the next five years and approximately AU$92 million in private sector investment.
This whole environment with design engineers, skilled operators and the right data all working together — it really makes a difference when it comes to accelerating our customer’s innovation cycles and time-to-market.”