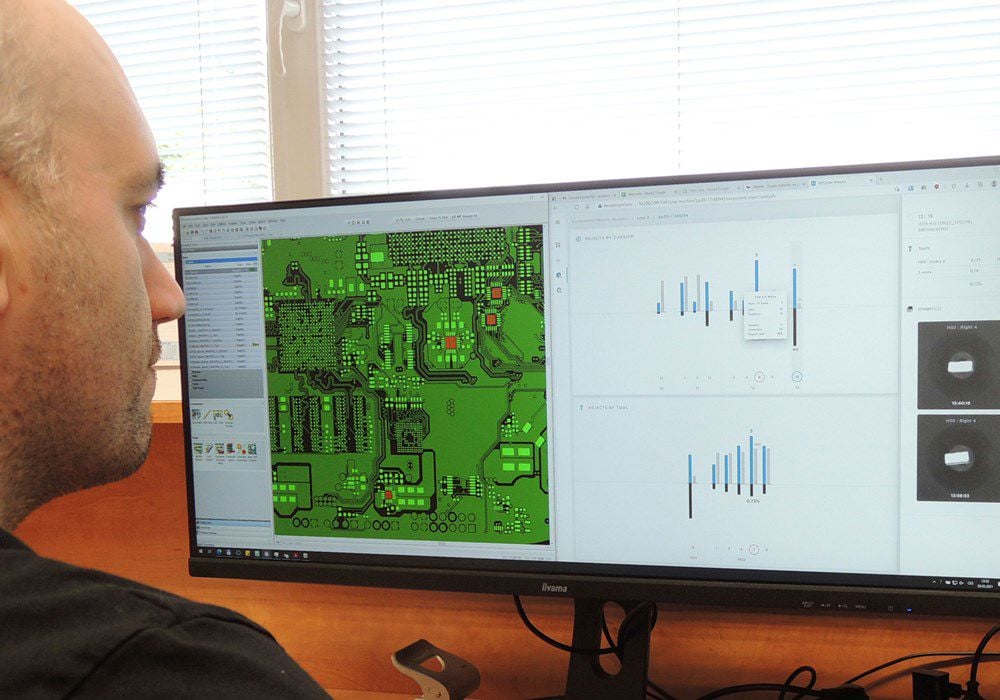
Analysis made easy
Taking actionable data from the production floor to the desktop
For a savvy production manager, it’s always possible to get the right troubleshooting data from your pick-and-place machine – if you have plenty of time and effort to spare. Thanks to MYCenter Analysis, the supervisors at one electronics manufacturing facility can get the statistics they need at a glance, without ever leaving the office.
Racom, with its dedicated technology center for SMT and hybrid assembly based in central Czech Republic, is focused on the development and production of equipment for wireless data transfer. As a specialist in small batches of complex boards, with cycle times averaging up to fifteen minutes, the company relies heavily on production managers with a passion for problem-solving.
Bringing data to the surface
“When overseeing production I’d typically have to investigate the data behind any rejects or stoppages in a web interface, which wasn’t particularly user-friendly,” explains Jaroslav Pernica, Production Leader at Racom. “MYCenter Analysis serves this data in a way that’s so much easier to act upon. Just by looking at the screen in my office I can see whether I need to go down to the production floor to check for specific errors.”
Pattern recognition
More than just simplifying an average workday, the software’s dashboard reveals patterns that lead to earlier and faster problem resolution. “What used to take ten or twenty minutes now takes a few seconds,” says Mr. Pernica “And when it’s a product we produce fairly regularly, I can see much further in advance if something has changed. The fact is actually pretty simple: it’s an easy-to-use off-the-shelf tool that saves me from having to dig through the data, machine by machine, on my own.”
Showing the way forward
For his colleague Zdeněk Bednařík, who is responsible for long-term production improvements, the reports generated by the MYCenter Analysis dashboard are particularly useful. “In the past, I would have to assume what the production bottleneck might be just based on experience,” says Mr. Bednařík “Now it’s visible for everyone. I can just bring up the reports and explain the changes we need to make to improve utilization. This makes it so much easier for everyone to be on the same page and devote their time to the right things –after all, it’s hard to argue with the facts.”