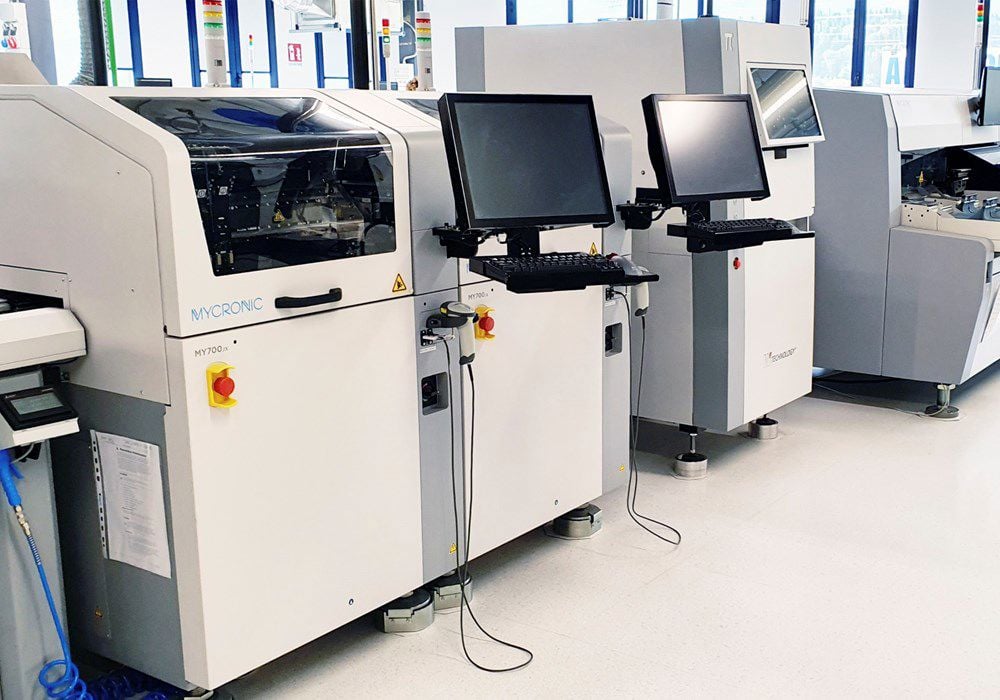
Mettre à profit les données de performance
Avec MYCenter Analysis, analysez les causes de vos rejets et améliorez l’équilibrage de votre ligne
Sous-traitant européen innovant, DF Elettronica est déterminé à continuellement repousser les limites de l’automatisation. Que ce soit pour l’inspection, la traçabilité, le transport de matériaux ou l’optimisation des processus, le recours à des technologies de pointe est, depuis de nombreuses années déjà, au cœur de la stratégie de production de l’entreprise. MYCenter Analysis est la dernière manifestation en date de cet effort visant à créer un environnement de production à la fois flexible et optimisé.
Située au nord de Florence, en Italie, DF Elettronica est une PME employant un peu plus de trente personnes. Mais en combinant les bonnes compétences avec les bonnes technologies de production, l’entreprise se démarque nettement de ses concurrents de taille similaire et adresse un large éventail de clients européens de premier plan dans le biomédical, l’éclairage et les télécommunications.
Investir dans l’agilité
"Notre dirigeant est un fervent partisan de l'automatisation des usines et de l'application des technologies de pointe", explique Patrizio Sorace, responsable de la production chez DF Elettronica. "Il a investi très tôt dans un four à chambre à vide, ce qui constituait un atout essentiel pour la fabrication de systèmes d'éclairage LED de haute qualité. Lorsqu'il a constaté que trop de temps était consacré au déplacement de racks de cartes depuis la ligne CMS vers l'assemblage final, il a investi dans des systèmes de transport autonomes. Il en va de même pour l’inspection 3D, les systèmes de marquage laser et les tests de sondes volantes, qui ont tous porté leurs fruits pour nos clients. Ainsi, lorsqu’il a entendu parler de MYCenter Analysis, il a immédiatement vu son potentiel pour économiser beaucoup de temps et d’efforts. »
Le besoin le plus urgent de la Production était une meilleure visualisation des performances du process pick-and-place. « En ce qui concerne l’équilibrage de l’utilisation des machines, nous cherchions un moyen plus rapide pour identifier où apporter des améliorations potentielles », raconte M. Sorace, expliquant que cela était particulièrement vrai pour leur ligne de production de plus grande série. " Certaines de ces séries peuvent occuper la ligne pendant plusieurs jours, de sorte qu’un gain de cinq ou six secondes par carte est vraiment significatif. "
L’autre objectif était d’identifier plus rapidement les raisons de rejets et de gaspillages de composants, qui demandaient trop souvent une analyse complexe des causes profondes. « Nous nous posions les questions suivantes : S’agit-il d’un problème de feeder ? D’un défaut du composant ? D’une buse sale ou cassée ? », dit M. Sorace. « Il y a des tonnes de variables, donc ce que nous voulions vraiment, c’était une sorte d’analyse statistique qui nous dirait, par exemple, si la majorité des problèmes étaient liés à une buse spécifique, ou à un composant particulier. »
La puissance de l’Analyse
M. Sorace et son équipe ont sauté sur l’opportunité d’être béta-testeur de MYCenter Analysis. « Nous étions vraiment heureux lorsque nous avons reçu la première version de MYCenter Analysis », dit-il. « C’était exactement ce dont nous avions besoin : un outil d’analyse statistique permettant aux opérateurs de trouver les causes des rejets. Maintenant, ils n’ont qu’à cliquer pour voir les images d’une buse et en tirer rapidement la bonne conclusion. Ou ils peuvent y accéder depuis leur domicile pour identifier une buse problématique, par exemple. Bien entendu, tous les problèmes ne sont pas résolus, mais nous faisons des progrès certains. »
Avoir un vue d’ensemble
Comme beaucoup de petites unités de production, M. Sorace et ses collègues ont un large éventail de tâches à gérer. En tant que responsable de production, M. Sorace supervise l’infrastructure, surveillant les performances globales des équipements et cherchant de potentielles améliorations du flux de production. À d’autres moments, il peut aider sur la ligne de production, programmer des composants ou effectuer d’autres tâches techniques. « C’est typique d’une usine comme la nôtre », explique-t-il. « Nous sommes tous tellement absorbés par de multiples machines et process qu’il peut parfois être difficile d’avoir une vue d’ensemble de la situation. C’est là qu’un logiciel comme celui-ci peut faire la différence, en nous donnant la vue d’ensemble statistique dont nous avons besoin. »
À l'avenir, le propriétaire de l'entreprise a proposé de confier un rôle plus important en matière de suivi et d'amélioration de la production à un contrôleur hors ligne - une responsabilité qui incombera très probablement à M. Sorace et à MYCenter Analysis. « Notre opérateur a tout simplement trop à faire », dit M. Sorace, « Alors maintenant je peux utiliser le logiciel pour l’aider. Je peux facilement imaginer une organisation pour la production de grande série, où chaque ligne a son propre opérateur dédié et où quelqu’un en dehors des lignes se concentre sur le monitoring, l’analyse et l’amélioration de la production. C’est ce que nous visons. »
Booster la performance
Lorsqu'on lui demande de quantifier les bienfaits de MYCenter Analysis, M. Sorace admet que cela peut être un challenge dans le cadre d'une production high-mix, où l'objectif est de continuellement gagner en contrôle sur une gamme infinie de variables. « Notre production varie tellement d’une tâche à l’autre qu’il est vraiment difficile de faire une comparaison avant-après », explique-t-il. « Et cette année représente une anomalie totale due à la pandémie, donc toute analyse comparative ne serait pas très réaliste. Mais notre expérience est que MYCenter Analysis nous a beaucoup aidé, en particulier en termes d’analyse des rejets et d’équilibrage de ligne pour les lots de production les plus importants. À long terme, nous l’utiliserons certainement pour créer des points de référence permettant de comparer les performances courantes avec les données historiques. Si nous pouvons continuer à accroître l’automatisation, à améliorer notre capacité à changer très rapidement de production quotidiennement, et à servir beaucoup de clients très rapidement avec un niveau de qualité élevé au coût le plus bas possible, alors nous savons que nous allons dans la bonne direction. »