Enter the control center
MYCenter Analysis elevates production performance to your dashboardCustomers asked, and we listened: Bringing together live performance data, root-cause analysis, and actionable insights into a powerful dashboard interface. It’s called MYCenter Analysis, and it’s all about improving production output with less operator intervention.
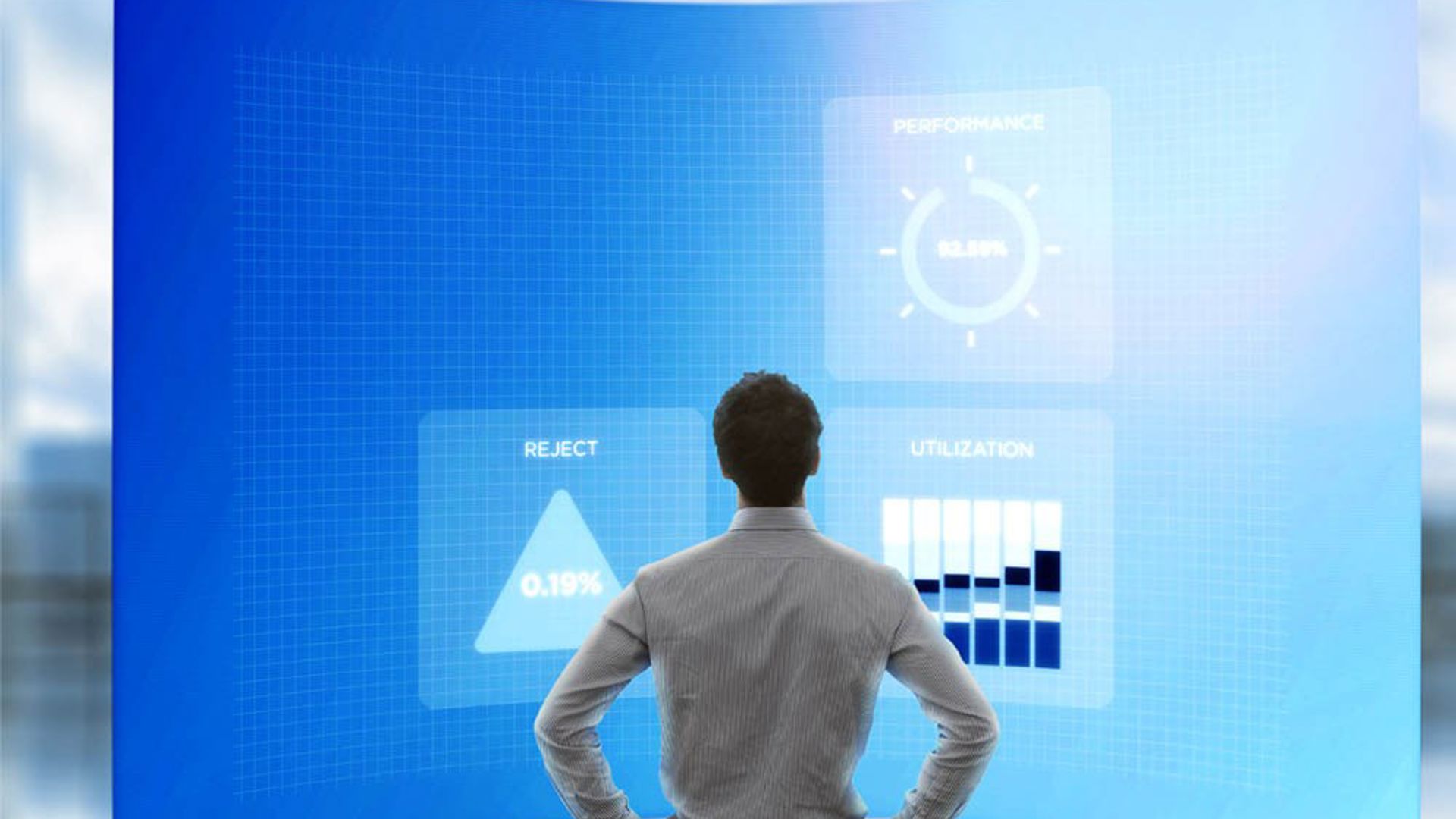
What tools do you need to better visualize performance, find root causes, and improve output in your SMT line? These were the questions that drove the development of MYCenter Analysis, Mycronic’s latest dashboard software.
The result of extensive co-development and beta testing, MYCenter Analysis is a promising example of the next generation of software interfaces being developed by the Mycronic 4.0 UX development team. Starting with the current pick-and-place control dashboard, the ambition is for MYCenter Analysis to become a comprehensive control center for production efficiency, encompassing a wide range of process steps.
Higher-level insights
Improved efficiency starts with the right data. In Live View, the new dashboard shows the current state of the line, number of boards produced, cycle time, efficiency, and workload balance. All this live data gives production engineers an overview of the most vital production statistics without the clutter of standard operational data. Directly from the web-based dashboard, it is now possible to compare current utilization with historical data, plan necessary interventions, and continuously refine production efficiency from anywhere, on any device.
Deeper problem-solving
Previously, reject rates and component waste might only be discovered after a job’s completion – sometimes hours, or even days, too late. With component mispick and reject analysis, MYCenter Analysis makes it possible to diagnose and resolve potential quality issues before they multiply. When an uncommonly high reject rate is discovered, production engineers can click through an extensive reject rate analysis, examine the data, and review detailed images of individual mountheads and components. The end result is a direct path from diagnosis to analysis to planned intervention - all from a single dashboard overview.
Thanks to detailed utilization data, potential bottlenecks can also be identified beyond the pick-and-place machines in both upstream and downstream production. With the right analysis, it’s possible to reveal issues including excessive waiting times for PCBs arriving in the line, solder paste issues detected in the Solder Paste Inspection system, or full PCB magazines at the end of the line, to name just a few. MYCenter Analysis makes this debottlenecking process faster, more effective and more thorough, thereby significantly reducing the need for trial-and-error diagnosis.
Better line balancing
As products and production processes grow more complex, effective line balancing has the potential to deliver huge productivity gains. MYCenter Analysis makes it easier to discover inefficiencies due to frequent machine stoppages as well as reduced speeds in the mounting or feeding of components and packages. In cases where MYPlan is not being used, the software can also highlight instances where a more optimal kitting setup might be possible.
Thanks to faster diagnosis of even the smallest problem areas, production managers can more effectively plan key steps and reduce machine stoppages to a minimum. Improved maintenance of component and package data, together with optimized feeder composition and loading, further contribute to more effective line balancing throughout the production process.
Faster results
Whether it’s enhanced remote monitoring, improved line balancing, or rapid reduction of unplanned downtime, the following use cases highlight some of the most immediate advantages offered by the new web-based dashboard control software.
REMOTE AWARENESS AND STRATEGIC PLANNING
Customer profile
Two production lines: One for large-batch OEM production, one for small-batch EMS production.
Previous challenges
- Sub-optimal line balancing
- Excessive unscheduled downtime due to unprepared feeders
- Lack of measurable improvements from process enhancements.
Advantages of MYCenter Analysis
- Improved line balancing due to MYCenter Analysis and MYPlan
- Reduction in unscheduled downtime
- Daily, weekly and monthly improvement monitoring via the desktop dashboard.
Expected benefits
Now possible to focus on and address the inefficiencies that the operators might not see in their daily work, preparing future production programs and staying close to customers. All without leaving the office.
RAPID JOB INTERVENTION AND RESOLUTION
Customer profile
High-mix, mid-volume contract manufacturing with regular repeat jobs of 500-1,000 boards on a single line.
Previous challenges
- Sudden drops in machine performance, reducing job output
- Often complex causes for reduced cycle time demanding further investigation
- Delayed awareness of machine performance drop causing long production delays.
Advantages of MYCenter Analysis
- Real-time monitoring indicating performance drop compared to historical job data
- Immediate visualization of lower-than-average cycle time
- Rapid intervention and investigation saving valuable production time
Expected benefits
Speed is critical when it comes to identifying an unusual drop in machine performance. Now no major problem goes unnoticed, which can save days in otherwise lost production output.
REDUCED COMPONENT WASTE
Customer profile
High-mix, mid-volume OEM production on a single MYPro Line.
Previous challenges
- Excessive component waste due to unresolved component rejections
- Lack of skilled operators able to quickly resolve tool or carrier issues
- Operators hesitant to stop production and perform root-cause analysis for rejects.
Advantages of MYCenter Analysis
- Real-time overview of current and historical reject rates
- Rapid identification of specific tools or carriers causing reject issues
- Reduction in component waste
Expected benefits
Significant reduction of component waste and unnecessary stoppages. Whenever there is waste it is now immediately identified and can be solved in a fraction of the time.