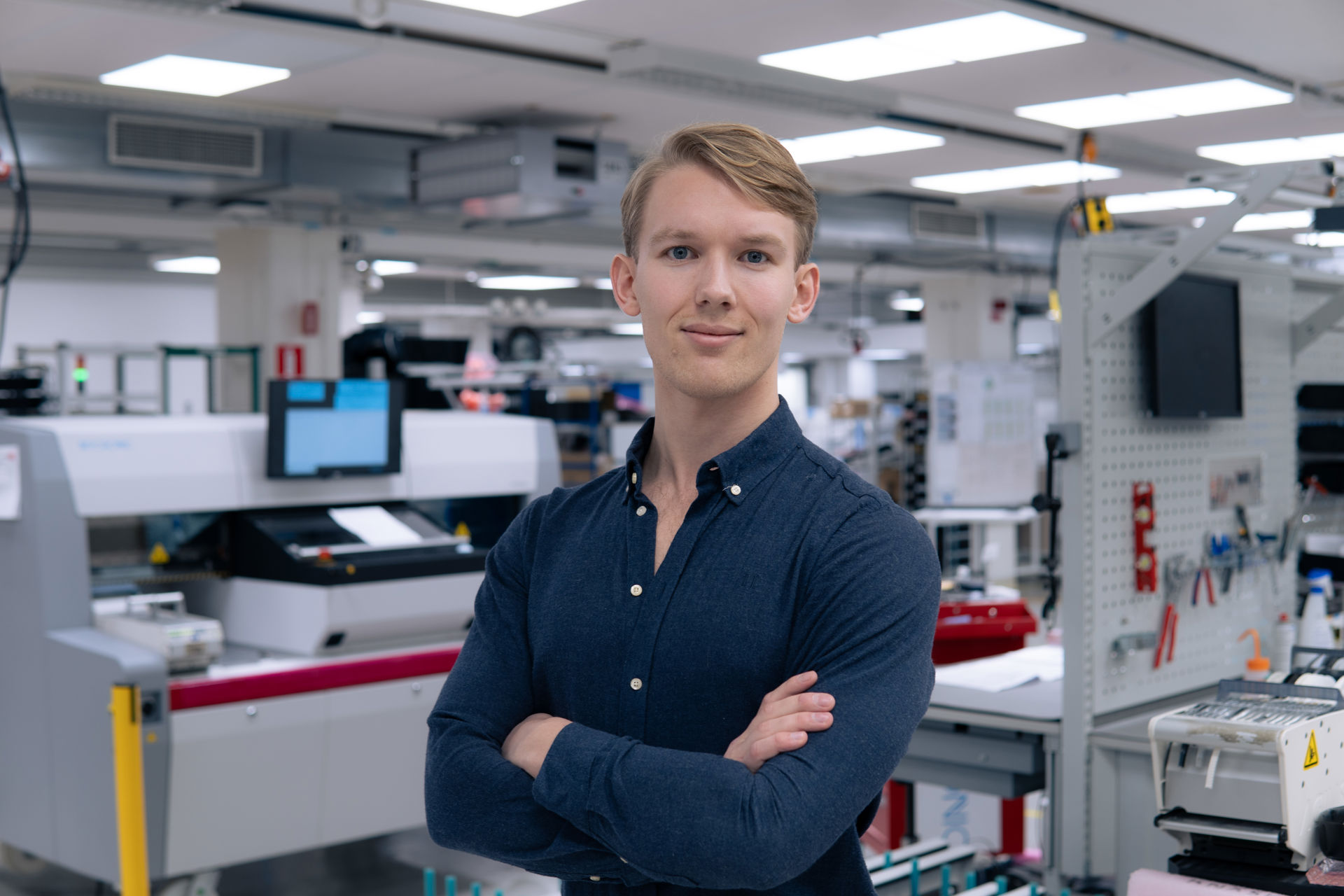
Going lean
How one Mycronic engineer is building a ‘lean’ production culture to radically boost output
Imagine significantly slashing production times while utilizing only half the floor space! Is that even possible?! Yes, according to Carl Jacobsson, 27, whose teams have achieved just this on key inspection equipment. As Group Production Manager at the Mycronic facility in Täby, Sweden he is implementing a “lean management” approach to reduce waste, adopt better processes, boost quality, safety and more.
From newbie to leader
Remarkably, in just four years, Carl transitioned from being a “new recruit” based in Stockholm to living and working abroad at subsidiaries in France and Germany where he got a hint of the company’s diverse international culture. Along the way, he helped lead the relocation of production to Sweden and currently spearheads the implementation of the “Mycronic Way” of lean production.
Young globetrotter
“I had just joined Mycronic and they asked if I wanted to go to France,” recalls Carl. “Who wouldn’t want to do that at as a young engineer? But that wasn’t all. A few years later I also went to Munich, Germany. In both places, the food, culture, people were great, and I learned so much. I may be unique at Mycronic for having worked for more than four months, twice, at two subsidiaries in such a short time.”
Regional flavors
“From day one, I got a flavor of the global culture at Mycronic: warm, diverse, and inclusive, yet with distinctive regional flavors. This is only natural in a global company, and it’s important to respect each other’s cultures. We all share a common goal – to bring massive value for the customer. This is where the lean thinking plays a crucial role, an idea that we borrowed from the automotive industry.”
Cutting out the fat
“When I onboard new recruits to my teams, I often discuss the concept of ‘lean meat’ and our efforts to trim fat in production,” Carl says. “People usually catch on to this analogy quickly: lean meat signals reduced fat content, increased protein and essential nutrients – all geared towards enhancing the value we bring to our customers.”
Overseeing a diverse team
Today, as first-line manager, Carl oversees three production teams at the assembly facility in Täby, just north of Stockholm. His responsibilities span three of the four production lines within the High Flex division, which focuses on production solutions and equipment for electronics production. These include Ejectors, used for ejecting solder paste and fluids on printed circuit boards; Inspection, which encompasses equipment for both Solder Paste Inspection (SPI), to inspect solder paste deposits, and Automated Optical Inspection (AOI), to inspect the components on the circuit boards; and Material handling, which involves solutions for material handling and component storage.
Continuous improvement
“The concept of lean thinking and processes is not new,” Carl points out, adding that he’s currently studying courses on this topic. “Lean management gained popularity through ‘The Toyota Way’ and the Japanese concept of kaizen or ‘continuous improvement.’ It’s all about maximizing customer value while minimizing waste. Everything should contribute to our customers’ satisfaction – whether it’s improved quality, processes or faster delivery times,” he explains.
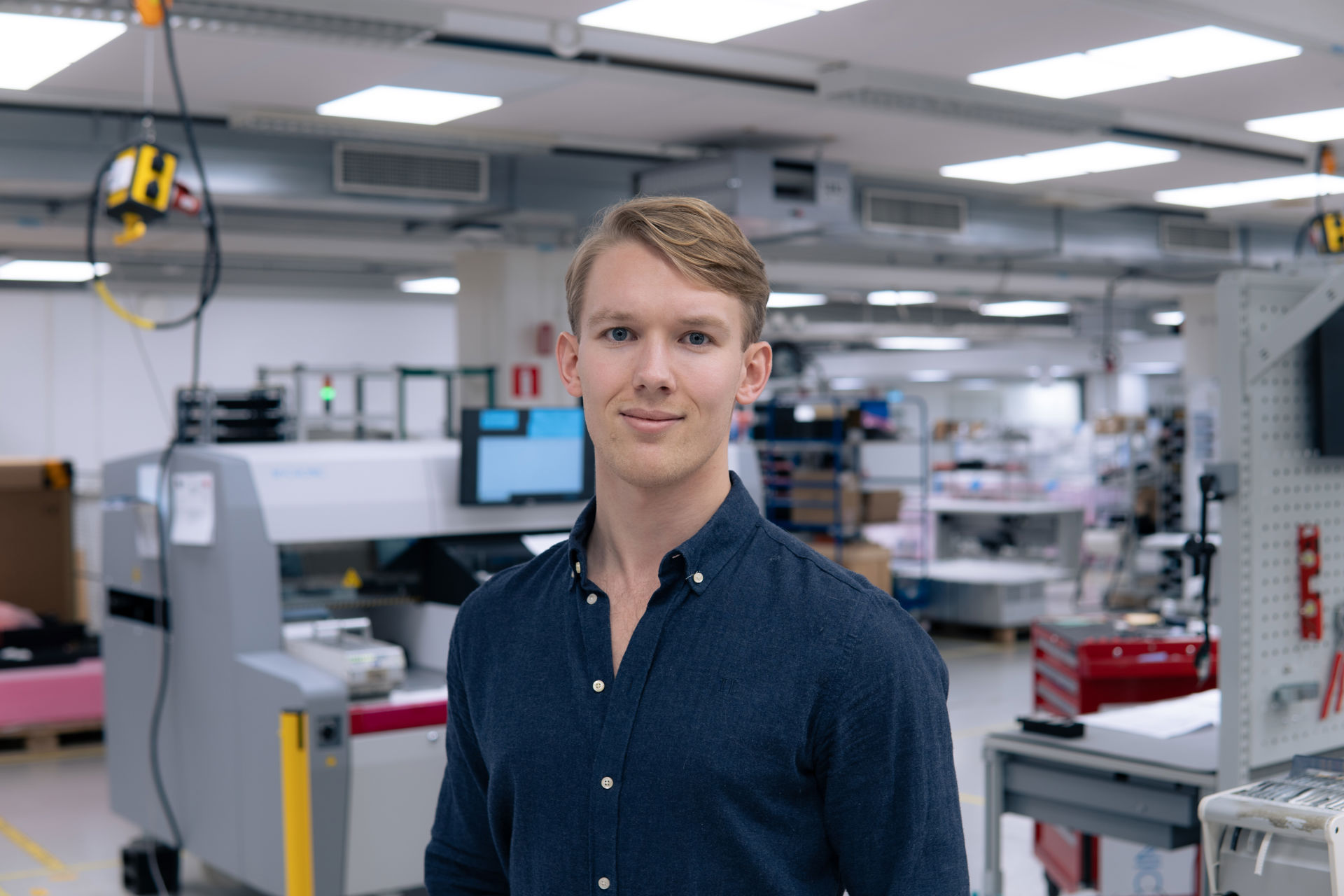
The concept of lean thinking and processes is not new. It’s all about maximizing customer value while minimizing waste. Everything should contribute to our customers’ satisfaction.
Big challenges, big love
Carl’s journey from graduation at Luleå Technical University, Sweden, with a MSc degree in Industrial and Engineering Management to his current leadership position at Mycronic is marked by significant challenges, lots of travels, and big love. While at university, he did internships at Scanfil, a contract manufacturer and systems supplier that builds the Hydra mounthead used on Mycronic pick-and-place machines. This early experience led to a consulting position at AFRY, the engineering consultancy, which offered him two job options: Scania or Mycronic.
Inspired to be at the forefront
“It was a tough choice,” recalls Carl. “Scania is a great company, but trucks are somewhat predictable. Ultimately, I felt inspired to join a company at the forefront of technology – a global company dedicated to bringing tomorrow’s electronics to life.” Although he joined the company in 2020, he admits to still be learning a lot about the many different products Mycronic’s equipment is used to manufacture. “Due to their complexity, it took some time to understand the value our machines create for customers. But once I grasped it, the experience became truly rewarding. Now, I feel aligned with Mycronics’s greater purpose,” he reflects.
Taking on the big challenges
According to Carl, one of his “superpowers” is taking on big challenges and finding ingenious solutions with his team. “Problem-solving is what I studied in school – the tougher, the better,” he says. “Here, team collaboration is vital.” Indeed, there was no shortage of challenges when he arrived at Mycronic amid a global pandemic. The company was also reorganizing its production in France and Germany.
In the shadow of the Alps
“Just imagine, as your first assignment, being sent to France for three months, initially to help out in production,” he recalls. “What a fantastic experience to work abroad in the foothills of the Alps, experience French culture and meet new colleagues and friends.” Specifically, he was in Saint-Égrève (near Grenoble), from where production of 3D AOI and SPI equipment later transitioned back to Täby in 2021. All in all, he spent five months in France.
A German love affair
A year later, Carl spent three months in Munich, Germany supporting the move of its production of component storage systems back to the Stockholm facility. While there, he met a lot of new friends, including his German girlfriend, who is now moving back to Sweden with him – “a big side benefit,” he says with a smile.
“Creating a feeling of ownership, team problem-solving and taking responsibility is the secret to success,” says Carl who is extremely proud of what his team has accomplished in the midst of a pandemic. They have substantially reduced manufacturing times of Mycronic’s SPI machines and camera assemblies for AOI, respectively, while utilizing less than half the required floor space, all thanks to “lean” principles.
Moving a mindset is tricky
“Anyone can balance a line, draw up a new floor plan, or decide how many workstations there should be,” Carl reflects. “The big challenge here was not only transferring the production but also instilling a mindset and lean culture. Moving production is easy; moving a culture and mindset is trickier.”
Leading the change
“It feels motivating to be working for a global, high-tech company that is leading important technology change in electronics. Our high-precision machinery is used for all sort of products that touch peoples’ lives,” he says.
“It's about ‘we’, not ‘me.’”
Looking forward, Carl says he will continue to accept the hard challenges on the road ahead. Successfully navigating these hurdles will require having a good company culture and maintaining an environment of innovation and curiosity. He underscores the importance of accountability and empowering everyone to make improvements, large and small. “The significant improvements are all about ‘we, not me’ – quality is everybody’s business,” he concludes.
Text: David Gray
ABOUT CARL JACOBSSON
Age: 27
Title: Group Production Manager (High Flex), Täby, Sweden
Education: MSc Production Engineering, Luleå University of Technology, Sweden
Unknown fact: “Gym rat” at university (six times a week)
Home: Grew up in Linköping, Sweden, partly on a horse ranch
Family: German girlfriend
Interests: Working out, soccer, traveling, skiing, spending time with friends
Favorite quote: “We are cutting the fat out of production to deliver value.”