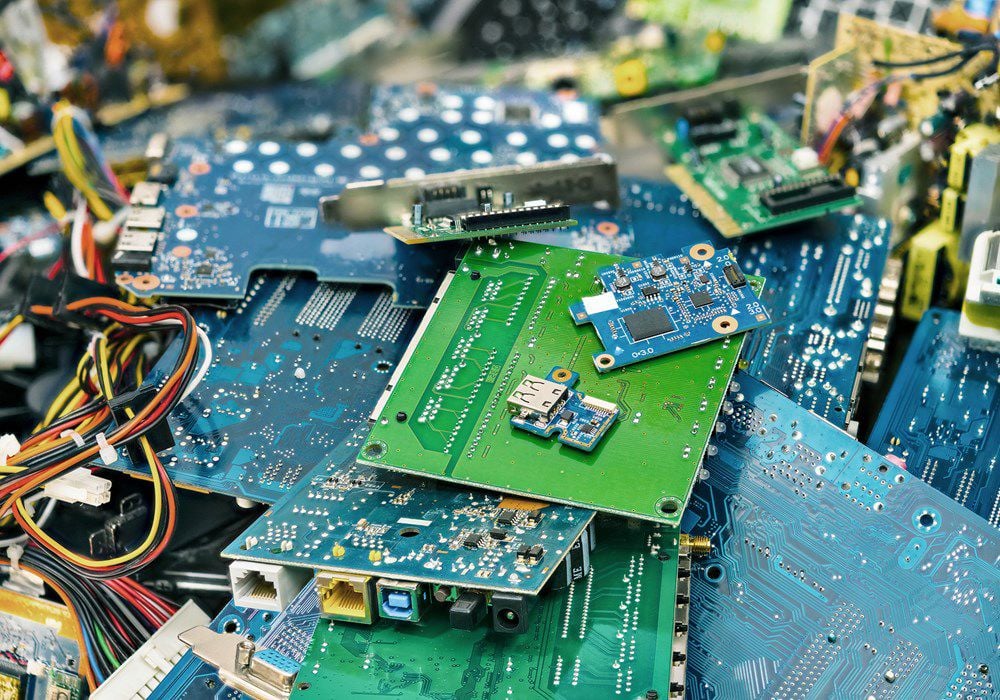
Reducing e-waste through innovation
Global consumption of electrical and electronic equipment is on the rise. When these products enter an end-of-life state, a large amount of the equipment becomes trash. E-waste, as it is called, is the world’s fastest growing waste stream due to not just higher consumption, but short life cycles and few options for repair. Meeting the rising demand for electronic products while ensuring the reduction of the products’ ecological footprint is one of the electronic industry’s biggest challenges.
According to the United Nations E-Waste coalition, global electronic waste is set to grow by 38% from 54 million metric tons in 2019 to 75 million metric tons by 2030 if current trends continue. To help address the e-waste challenge and grasp the opportunity of the circular economy, Mycronic is starting at the design stage. By focusing on an area where we can impact the reduction of e-waste, - namely: innovation for sustainability, Mycronic aims to promote circularity in the industry by starting with our own products.
Effectivizing end-of-life treatment
By using less materials in our products and by facilitating dismantling, we simplify recycling for the customer. Additionally, Mycronic aims to reduce materials used in production by focusing on maintenance and upgrades to further extend the useful life of our equipment. To support these efforts, Mycronic has developed a method for product Life Cycle Analysis (LCA), which has thus far been used within two product segments. The LCAs, which offer detailed information about the environmental impact of the products, are now influencing the product development paths in tangible ways.
Waste reduction through manufacturing improvements
Through developing and selling equipment that improves production efficiency, Mycronic can reduce waste of resources during manufacturing. For example, our jet printer has been developed to reduce the waste of solder paste during use by the customer and we continually develop efficiency improvements of our inspection machines, which allow for faults to be detected earlier in production runs.
Close up of a jet printer ejector
Improving circularity through repurchasing programs
While reducing materials used in production is an important factor in reducing e-waste, contributing to circularity of the materials used is another aspect to consider. Mycronic’s complex products contain many different materials and components. The purchase of materials for manufacturing these products represents about 10 percent of our carbon footprint. In our efforts to reduce this number, we have taken a holistic approach. This means that in addition to innovating the manufacturing process to ensure that less materials are used, we are committed to make continuous efforts toward improving circularity. For example, two of our divisions have repurchase programs where old equipment is renovated and upgraded to be sold again.
By adopting this holistic approach, Mycronic aims to sustainably bring tomorrow's electronics to life.