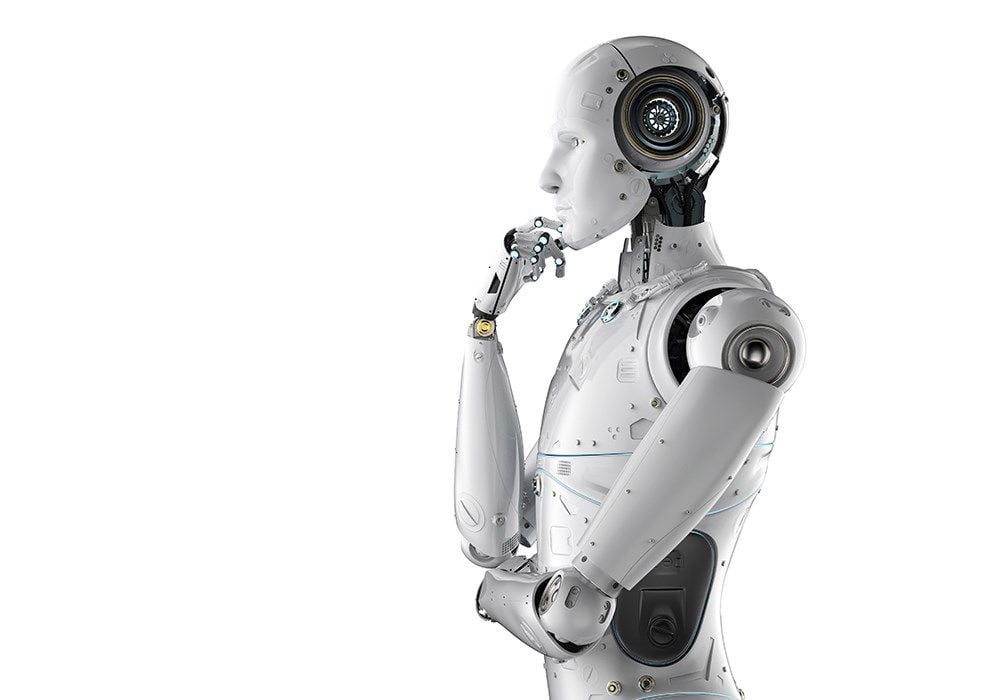
Empowering people through automation
How smarter human–machine collaboration is making your people more valuable than ever
Even with all your resources running at full capacity, there are still significant gains to be made. Through enhanced interfaces and smarter interactions, your people can focus on the higher-value tasks that make your factory more agile and more productive.
IN RECENT YEARS, factory-wide productivity has been boosted significantly by smarter production solutions, with Mycronic contributing increasingly integrated optical inspection, jet printing, pick-and-place and material handling systems. Automated solder paste repair and inspection modules have essentially eliminated screen printing compromises. Intelligent, self-replenishing material handling systems have rapidly reduced kitting and changeover times and enabled one hundred percent stock accuracy. And the fully integrated MYPro Line is constantly introducing new capabilities and process insights. Each of these advances has helped customers achieve higher throughput with the same installed base at lower costs.
Now, thanks to rising volumes of real-time process data, Mycronic is unlocking new ways to help people and machines work better together.
From unrefined data to accurate results
Handled properly, inspection data holds enormous potential for future quality and productivity gains. Made available to other machines, it can create closed-loop systems to enable auto-correcting processes. Connected to robotic systems, it can request autonomous assistance. Communicated to process engineers, it can assist deeper root cause analyses and preventive action. And on the highest levels of process control, it can be used to simulate the quality of a new product before the first batch is even produced. Where quality control was once seen as an end verification, it’s now about producing fewer defects in the first place.
Next-generation machine learning through AI
Thanks to advances in deep learning, production staff are already benefiting from rapidly improving software capabilities. Most recently, research at the Center for Deep Learning in Electronics Manufacturing has been focused on training deep learning algorithms with thousands of sets of real production data. The aim is to develop new adaptive methods of automated production, image processing and auto-programming throughout the SMT line. For example, new functionality based on machine learning has recently been released on Mycronic’s range of 3D AOI systems. Based on an automatic component recognition algorithm and automatic teach functionality, the new software tools assist process engineers in creating new 3D inspection programs in as little as half the previous programming time.
Unlocking the potential of people
The advent of AI — when combined with advanced robotics and software capabilities — represents a huge opportunity to upskill production staff and implement new agile manufacturing strategies. “It’s easy to see automation as only about reducing manual labor,” says Göran Frank, Product Manager Industry 4.0 at Mycronic. “But the real question is: How can we all use these new tools to make our work more engaging and more productive? Our philosophy has always been to find new ways for machines and humans to collaborate better. Ways to simplify programming, shorten changeover times and eliminate manual rework. Ways to make people more valuable — not less. Even hard-to-automate tasks like reel handling, kitting and distribution can now be vastly reduced thanks to collaborative robotics systems we’re beginning to implement. These are the kinds of future bottlenecks we’re starting to eliminate, and it’s really empowering the people on the factory floor.”