Impossible Deadline, Intelligent Solution
How Axxon built a complex smart driving domain controller assembly line in 45 DaysIn the fast-paced world of smart driving technology, Axxon Mycronic faced a significant challenge: building a complex smart driving domain controller assembly line in just 45 days. This article explores their innovative solutions and collaborative efforts that set new industry standards for safer, smarter mobility experiences worldwide.
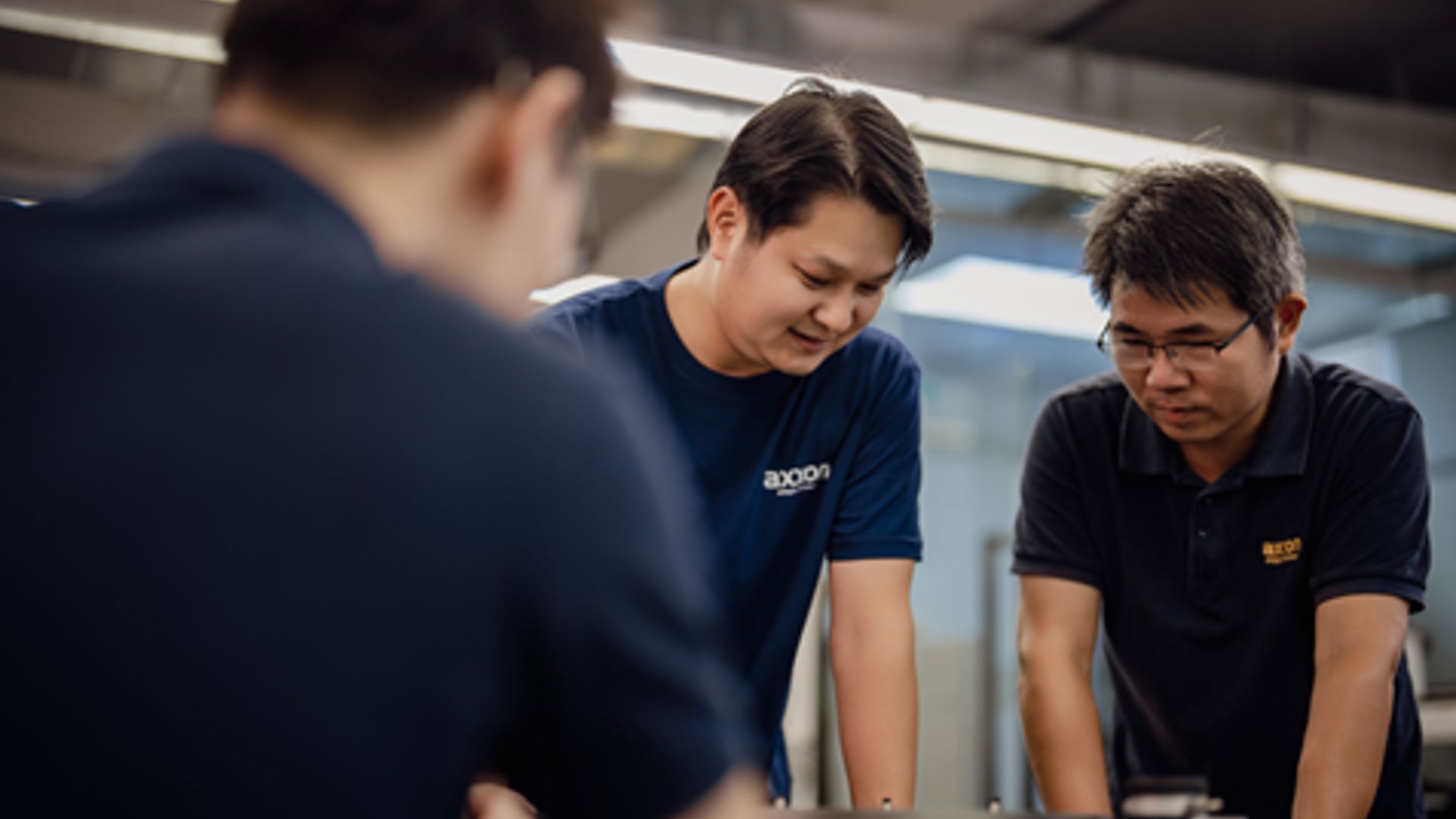
With the deep integration of artificial intelligence and automotive technology, smart driving is sparking a global revolution in transportation. To ensure vehicles can autonomously navigate various environments safely, accurately, and swiftly—surpassing human reliability—it requires top-tier sensors, powerful computing capabilities, intelligent algorithms, and ultra-high security. Any weak link in this chain could lead to safety incidents.
One of the leading automotive manufacturers in this field has been pursuing the most advanced solutions. Headquartered in Shenzhen, China, Mycronic's High Volume division, Axxon Mycronic addressed an urgent technical challenge for them.
Complex processes vs. Extreme deadlines: The assembly line race
The smart driving domain controller is the "super brain" of intelligent vehicles, primarily responsible for centralized processing of perception, decision-making, and control tasks related to autonomous driving. It must integrate massive data from multiple sensors within milliseconds, achieve precise decision-making control through high-performance chips and safety-redundant algorithms, and meet stringent requirements for continuous functional upgrades and adaptation to complex scenarios.
A leading automotive manufacturer approached Axxon with a near-impossible challenge: "We need five assembly lines for domain controllers, and the first one must be operational within two months. This is critical to our vehicle delivery timeline."
This complex assembly line involves multiple processes. Through past collaborations, the manufacturer had witnessed Axxon's decade-long expertise in dispensing, coating, inspection, and other techniques.
"This was our first project of such high complexity, with a delivery cycle far shorter than industry standards," said Axxon's project leader.
Rapidly breaking down the processes was key. The assembly line included over 10 techniques such as underfill, coating, inspection, curing, and RTV. Axxon's divisions—Precision Dispensing, Coating, Industrial Dispensing, and Smart Assembly—quickly reached a consensus on the overall design. They also forged a strategic partnership with external suppliers for the first time to swiftly resolve issues and minimize project delays.
Turning Challenges into Opportunities: The Miracle Journey
"From the very beginning, they came prepared with comprehensive equipment configurations and staffing plans, capturing every detail of our needs during communication. The entire collaboration felt like a green channel," remarked one of the automotive manufacturer's executives, deeply impressed by Axxon's professionalism.
Axxon's project leader reflected, "This was no easy task, but we gave it our all to make it happen—the client's needs always come first."
To tackle the challenge of integrating multiple processes, Axxon's cross-departmental teams swiftly designed a standardized device: the AI350 dual-head dual-station platform. It could handle underfill, coating, adhesive fixing, and other processes interchangeably by simply swapping dispensing valves.
The project leader added, "A shared software platform was also essential. Our software achieved 98% reusability—users could select specific processes to quickly build a workflow. Identical processes could be replicated across machines, reducing debugging time by 70%."
"We wanted minimal human intervention for maximum efficiency, and Axxon delivered perfectly," the manufacturer said with delight. "In practice, the equipment's master control scanning function automatically adjusted rail width with a precision of ±0.1mm, boosting efficiency by 80% compared to manual adjustments. This was an unprecedented experience for us."
Axxon's project leader explained, "Intelligent equipment is another pillar of efficiency. Using the MES system, we built a shared data platform to upload critical quality parameters and images in real time, ensuring full traceability. It also enables remote monitoring and troubleshooting."
"Now, Industry 4.0 isn’t just a concept—it’s our daily reality," remarked Axxon's team leader. The assembly line adopted a cutting-edge "lights-out factory" model, with AGVs (Automated Guided Vehicles) handling material transport, nearly eliminating human intervention.
Axxon delivered the first line in 45 days and the remaining four within the next two months. "The speed and output far exceeded our expectations!" the manufacturer exclaimed. "Thanks to Axxon's full support, our vehicles rolled out on schedule."
Responsive Support Is Everything: Blazing Speed, Heartfelt Service
Reflecting on the assembly line's setup, the manufacturer said, "We initially expected the equipment to be operational within 10 days of arrival, but they assembled a complete line in just 3 days. Within three weeks, it was unbelievable in mass production!"
Axxon's project leader explained the speed: "Before arriving on-site, we rehearsed the entire assembly process internally. After receiving the client's samples, we pre-programmed the software and debugged parameters to minimize on-site adjustments. The universal design of our products also accelerated installation."
Axxon's technical support team was involved from the outset to ensure a thorough understanding of project requirements. For each process segment, Axxon deployed TPM+PM specialists, software engineers, and on-call external suppliers for immediate issue resolution.
"Delivery is just the starting point of service, not the end," Axxon emphasized. Their technical lead added, "We want clients to feel our professionalism and dedication. From day one, we prepared training materials, operation manuals, standard machine parameters, production guidelines, and detailed maintenance schedules to ensure seamless operation by the client's team."
"In the future, we plan to use this line for more products. Axxon anticipated this—their machines accommodate varying product widths and intelligently adjust process parameters. Partnering with Axxon was the best decision we could have made," the manufacturer said.
Smart Driving Future: Axxon Is Ready
Smart driving is not just a technological breakthrough — it is an upgrade opportunity for the entire automotive supply chain.
Leveraging its robust R&D platform, Axxon provides comprehensive one-stop solutions for the automotive electronics industry. These include 3D coating film inspection with ±2-micron precision, industry-leading low-pressure screw valves to prevent silicone oil leakage, and core solutions like >=120UPH dispensing-assembly-inspection lines for automotive parts.
Today, Axxon has established overseas offices and subsidiaries in key markets such as the Netherlands, the U.S., Mexico, South Korea, and Thailand. It collaborates deeply with mainstream NEV manufacturers — literally, one out of every five NEVs sold globally uses Axxon's technology.
Moving forward, Axxon will continue partnering with industry leaders, empowering smart vehicle manufacturing with innovation to deliver safer, smarter mobility experiences worldwide.
Read more about products and solutions from our Axxon Mycronic's High Volume division here: Advanced Dispensing and Coating Solutions | Mycronic